Hay Baler Maintenance Costs and How to Reduce Them
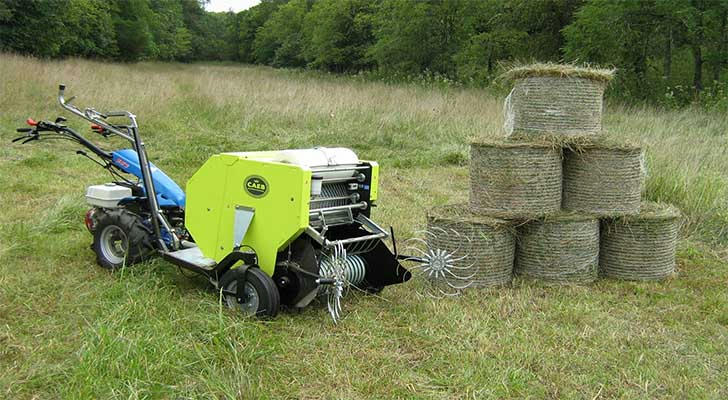
Hay balers are essential machinery in farming, enabling farmers to efficiently harvest and package hay for animal feed. However, maintaining these machines incurs costs that can accumulate over time. Properly managing these maintenance costs and reducing daily operating expenses is crucial for maintaining farm profitability. In this article, we will break down the maintenance costs of hay balers and explore specific strategies for reducing these costs.
1. Common Maintenance Costs of Hay Balers
The maintenance costs of hay balers typically fall into these categories:
• Routine Inspections and Upkeep: Regular inspections are necessary to ensure the baler runs smoothly. This includes tasks like replacing lubricants, filters (air, fuel, hydraulic), and checking hydraulic systems. The cost of consumables like oils and filters can add up.
• Mechanical Part Replacements: Over time, components such as belts, chains, tires, and baling twine wear out due to constant use. These parts need to be replaced periodically, which adds to the maintenance costs.
• Labor Costs: Repairs and regular maintenance require skilled technicians. Labor costs can include technician wages and costs associated with transporting the equipment to the workshop or handling downtime.
• Storage and Transport Costs: Storing hay balers properly requires space, and transporting the equipment for maintenance or temporary storage can also incur extra costs.
2. Factors Affecting Maintenance Costs
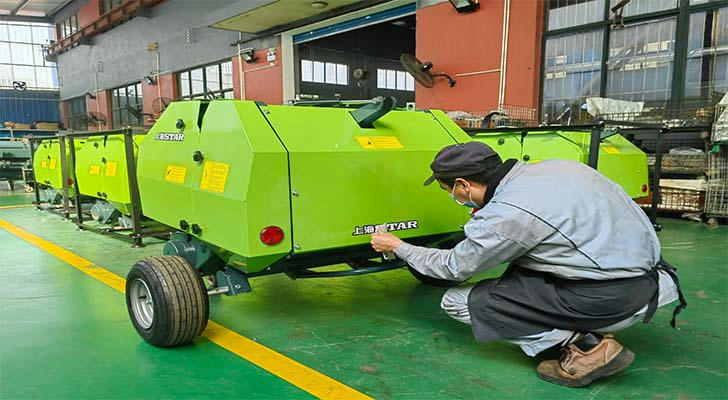
Several factors influence the overall maintenance costs of hay balers:
• Usage Frequency: The more frequently a baler is used, the higher the maintenance costs. Heavy use during peak harvesting seasons causes parts to wear out faster, which increases the frequency of repairs.
• Brand and Model: Different brands and models of hay balers have varying maintenance requirements. Higher-quality brands or more advanced models often have lower long-term maintenance costs due to better durability.
• Operating Environment: Machines that operate in dusty, humid, or harsh environments tend to experience higher wear and tear, leading to more frequent repairs.
• Operational Practices: Improper operation or neglecting maintenance can accelerate equipment wear. Providing training to operators can help prevent errors and reduce damage, lowering repair costs.
3. How to Reduce Daily Operating Expenses
To reduce daily operating expenses and extend the life of hay balers, here are some actionable strategies:
• Perform Regular Preventive Maintenance: The best way to avoid costly repairs is by conducting regular inspections and maintenance. Ensure that key parts like filters, belts, and chains are checked and replaced before they fail. A simple preventive approach can extend the machine's life and prevent expensive breakdowns. Set up a maintenance schedule (e.g., weekly checks, seasonal inspections) and track the usage of each baler to predict when parts may need replacement.
• Train Operators Effectively: Proper operator training is vital. Ensuring that operators know how to handle the baler correctly and how to spot early signs of wear can reduce costly mistakes. Training on machine usage, proper adjustments, and routine cleaning can significantly reduce operational wear. For instance, training operators to recognize early signs of belt slippage can prevent larger breakdowns.
• Invest in High-Quality Equipment: While high-end hay balers might come with a larger initial cost, they are often more durable and efficient. They require fewer repairs and consume less fuel over time, saving money in the long run. Choose models that are known for their reliability, and look for ones with features designed to reduce wear, such as reinforced parts and self-lubricating systems.
• Optimize Usage and Minimize Idle Time: Use the hay baler efficiently by planning work schedules to avoid excessive idle time. Running the baler only when needed will reduce unnecessary wear and tear. For example, during off-peak seasons, consider storing the machine in a sheltered area to protect it from the elements and reduce wear from environmental factors.
• Keep Machines Clean: Regularly clean the baler to avoid dust and debris buildup, which can cause overheating or clogging of parts. Clean the cooling systems, check the bearings, and remove any accumulated material. A simple cleaning routine can extend the life of components such as hydraulic systems and cooling fans.
4. Using Energy-Efficient Equipment to Reduce Operating Costs
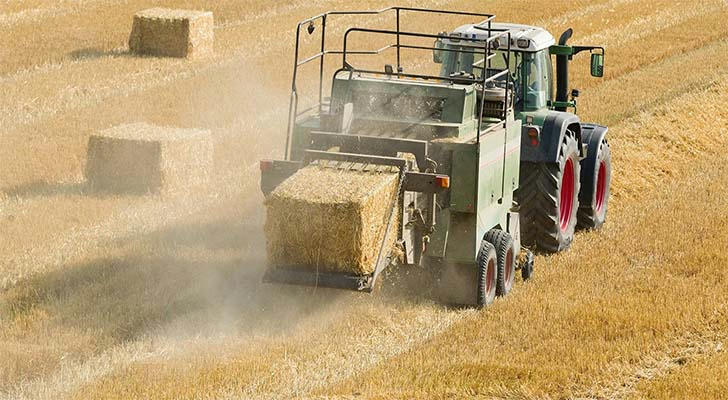
Modern hay balers are becoming increasingly energy-efficient, which can significantly lower operating costs. While energy-efficient models may have a higher initial purchase price, the long-term savings are substantial due to reduced fuel and energy consumption.
Energy-efficient balers use advanced technologies like optimized hydraulic systems, low-energy motors, and intelligent power management systems that reduce fuel consumption and maintenance costs. These innovations not only save money but also reduce environmental impact, which is an important consideration for sustainable farming.
For example, energy-efficient models could save 10-15% on fuel costs over the course of a year, depending on usage. Additionally, by reducing wear on components, these machines often have a longer service life, further lowering long-term costs.
5. Conclusion
Maintaining a hay baler can be costly, but by implementing the right strategies, farmers can significantly reduce these expenses. Regular preventive maintenance, proper operator training, investing in durable equipment, and optimizing usage are all effective ways to lower daily operating costs.
Choosing energy-efficient machines may require a larger upfront investment, but the savings on fuel, maintenance, and environmental impact make them a smart choice for long-term cost reduction.
To summarize, a proactive approach to maintenance, combined with careful equipment selection and efficient use, will ensure that your hay balers operate at peak efficiency while minimizing costs. Tracking usage, setting maintenance schedules, and investing in high-quality, energy-efficient machines will provide clear financial benefits and contribute to a more sustainable and profitable farming operation.